Westinghouse unveils 'industry first' with 3D-printed component
.jpg)
Additive manufacturing - or 3D printing - simplifies the manufacturing process by building a three-dimensional object from a computer-aided design model, usually by successively adding material layer by layer. Westinghouse Chief Technology Officer Ken Canavan says this enables the company to offer its customers enhanced component designs that improve performance and reduce costs, as well as to provide access to components that may not be available using traditional manufacturing methods.
Ken Petersen, Exelon Generation's vice president of nuclear fuels, described additive manufacturing is an exciting new solution for the nuclear industry. "The simplified approach helps meet the industry's need for a wide variety of low-volume, highly critical plant components," he said.
Westinghouse has been pursuing the use of powder bed fusion - an additive manufacturing technique that uses either a laser or electron beam to melt and fuse material powder together, layer by layer - "for applications including complex and next-generation components required for performance gains; obsolete and difficult-to-procure components; and unique components such as prototypes, mockups and tooling".
_77790.png)
_59102.jpg)
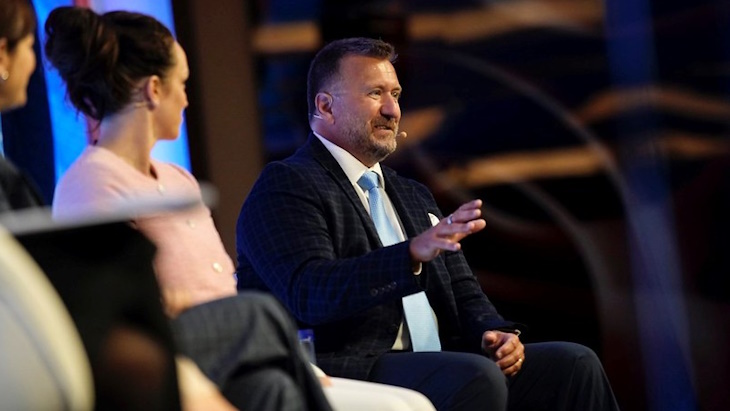
_49833.jpg)
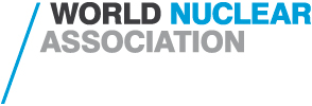