GNF lead test assemblies ready for loading
Lead test assemblies of accident-tolerant boiling water reactor fuel have been shipped to Southern Nuclear Operating Company and will be installed in an operating reactor, Global Nuclear Fuels (GNF) announced yesterday. The IronClad and ARMOR assemblies will be loaded into the Edwin I Hatch plant.
![]() |
Hatch (Image: NRC/Southern Nuclear) |
The IronClad lead test assemblies will be the first developed through the US Department of Energy's (DOE) Enhanced Accident-tolerant Fuel programme to be installed in a commercial nuclear reactor.
GNF is working with Southern Nuclear and Exelon Generation to insert lead test assemblies using an iron-chromium-aluminium fuel cladding material, known as IronClad, and coated zirconium fuel cladding, known as ARMOR, into reactors.
ARMOR coating is applied to a standard zirconium fuel rod. It provides enhanced protection of fuel rods against debris fretting, and greater resistance to oxidation, than standard zirconium cladding. It also shows "superior material behaviour over a range of conditions", GNF says.
IronClad material is designed to provide oxidation resistance and "excellent material behaviour" over a range of conditions, with low oxidation rates of at higher temperatures further improving safety limit margins, the company says. In addition to developing the assemblies for insertion, GNF has been working with suppliers to establish robust fabrication processes for the cladding and with utilities, national laboratories and other fuel vendors, to assess the economic benefit of ferritic steel-clad fuel rods and advanced technology fuel solutions more generally.
Two variants of IronClad material will be installed at Hatch: one will be in a fuel rod form but will not contain fuel, while the other will be in the form of a solid bar segment. ARMOR lead test assemblies that contain fuelled rods will be installed in the same reload. Lead test assemblies containing fuelled versions of both rods are planned to be installed at Exelon's Clinton power plant in 2019.
"Accident-tolerant fuel technology offers superior safety margin to address a beyond design basis event and the potential for more cost-effective operation of the existing boiling water reactor fleet," GNF CEO Amir Vexler said. The company is exploring many technologies for its advanced fuel portfolio but believes that its expertise and experience with ferritic steel and coated zirconium cladding will enable it to provide an enhanced solution to customers more quickly, he said.
Hatch, a two-unit boiling water reactor in south-western Georgia, is owned by Georgia Power, Oglethorpe Power, MEAG Power and Dalton Utilities, and is operated by Southern Nuclear. GNF is a GE-led joint venture with Hitachi and operates primarily through Global Nuclear Fuel-Americas in Wilmington, North Carolina, and Global Nuclear Fuel-Japan Co, in Kurihama, Japan.
Game-changer
The DOE's programme to develop accident-tolerant nuclear fuel was launched in 2012, with the aim of developing new cladding materials and new fuel materials that can better tolerate the loss of active cooling in the core, while maintaining or improving fuel performance and economics during normal operation.
Three concepts for advanced fuels are under development and qualification, with three fuel vendors - GNF, Framatome and Westinghouse - supported by shared funding from the DOE. Framatome's concept involves using a chromium-coated zirconium alloy cladding combined with chromia-doped fuel pellets, while the initial phase of Westinghouse's EnCore Fuel product consists of coated cladding containing uranium silicide pellets.
Independently of the DOE programme, US-based Lightbridge is working to develop an accident-tolerant advanced metallic fuel, recently launching the Enfission joint venture with Framatome to commercialise it.
Accident-tolerant nuclear reactor fuels are a potential game-changer for the industry, the US Nuclear Energy Institute (NEI) said yesterday. The capabilities of these more robust fuel designs are showing enough promise that the US nuclear industry wants to accelerate their development and possible deployment, and the industry is working towards phased deployment in a commercial reactor in the early to mid-2020s, it said.
"This schedule is of key importance in the decisions our members will need to make when evaluating the ATF [accident-tolerant fuel] safety benefits against the costs of adopting this technology," NEI technical advisor Andrew Mauer said in a comment letter to the US Nuclear Regulatory Commission this week. The NEI called for a "more transformational shift" in the NRC's approach to fuel licensing in order to license accident-tolerant fuels, and suggested that the NRC could leverage the DOE's existing advanced modelling and simulation capacity to support the licensing process.
Researched and written
by World Nuclear News
_49098.jpg)
_57190.jpg)
_70526.jpg)
_75453.jpg)
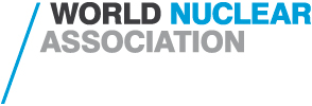